鋼套作為機(jī)械傳動(dòng)中的關(guān)鍵耐磨部件,其表面硬度與變形量直接影響配合精度與服役壽命。高頻淬火通過(guò)精準(zhǔn)熱控制與創(chuàng)新防變形設(shè)計(jì),可在鋼套表面形成 0.5-3mm 硬化層(硬度 50-60HRC),同時(shí)將變形量控制在 0.05mm 以內(nèi),滿足精密機(jī)械的裝配要求。
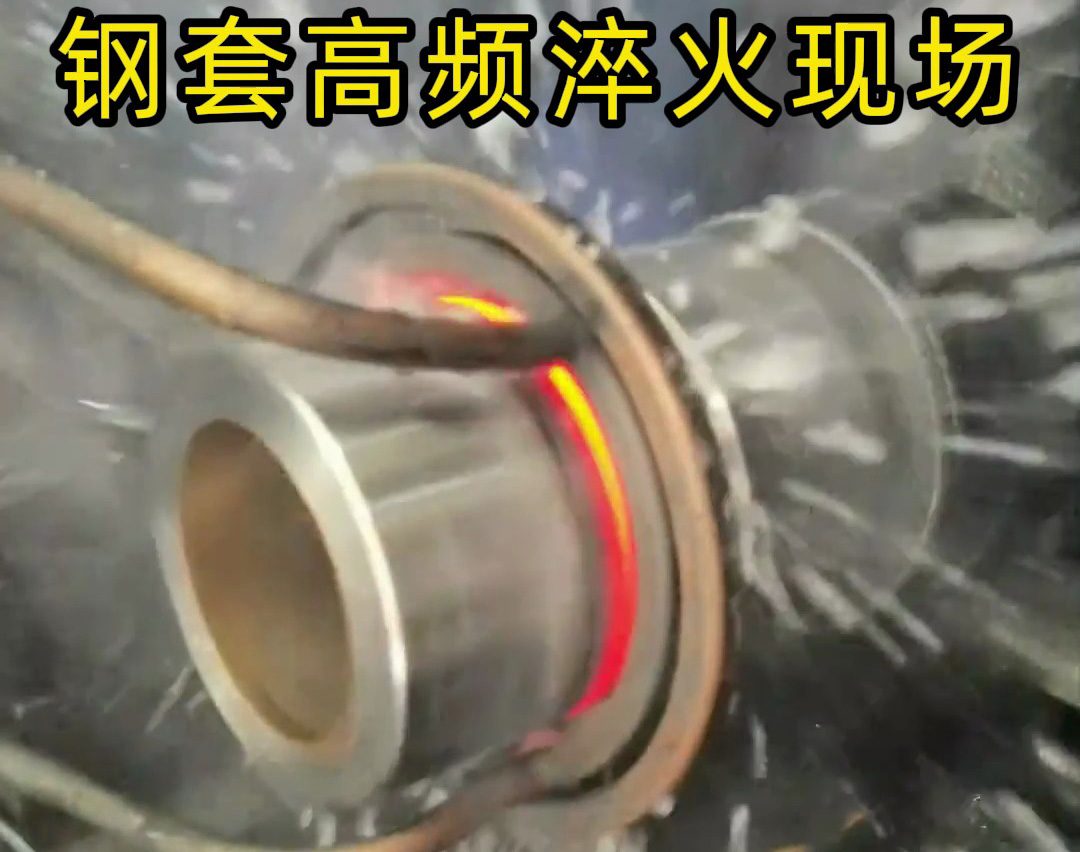
高頻電流(30-800KHz)通過(guò)定制感應(yīng)器時(shí),在鋼套表面產(chǎn)生渦流效應(yīng),熱量集中于表層 0.1-3mm 區(qū)域(趨膚深度可控)。以 45# 鋼套為例,200KHz 高頻磁場(chǎng)可使 Φ50mm 鋼套表面在 15 秒內(nèi)升溫至 850℃,而心部溫度維持在 200℃以下,通過(guò)表層快速淬火(噴水或油冷)形成馬氏體硬化層,心部保留韌性。
鋼套淬火變形源于熱脹冷縮產(chǎn)生的內(nèi)應(yīng)力,通過(guò)以下方式控制:
梯度加熱:分階段升溫(如先 60% 功率預(yù)熱,再 100% 功率加熱),減少溫差應(yīng)力;
對(duì)稱加熱:環(huán)形感應(yīng)器確保周向溫度均勻(溫差≤5℃),避免局部過(guò)熱變形;
動(dòng)態(tài)冷卻:旋轉(zhuǎn)噴淋冷卻(轉(zhuǎn)速 50-100rpm)使淬火介質(zhì)均勻覆蓋,降低冷卻不均應(yīng)力。
根據(jù)鋼套尺寸與硬化層需求,感應(yīng)器采用差異化設(shè)計(jì):
鋼套規(guī)格 | 感應(yīng)器類型 | 頻率選擇 | 硬化層深度 |
---|
Φ10-30mm | 單匝空心線圈 | 400-800KHz | 0.5-1mm |
Φ30-80mm | 多匝密繞線圈 + 導(dǎo)磁體 | 100-300KHz | 1-2mm |
Φ80-200mm | 分段式組合線圈 | 30-100KHz | 2-3mm |
案例:某汽車變速箱 Φ60mm 鋼套,采用 200KHz 雙匝線圈 + 導(dǎo)磁體,加熱 18 秒后噴水淬火,硬化層深度 1.2mm,圓周硬度差≤2HRC,橢圓度變形 0.03mm。
旋轉(zhuǎn)速度:根據(jù)鋼套直徑調(diào)整(Φ50mm 以下 100rpm,Φ50-100mm 80rpm),確保周向冷卻均勻;
冷卻介質(zhì):水基淬火液(濃度 5-10%),沸點(diǎn) 105-110℃,既保證淬火烈度,又減少蒸汽膜效應(yīng)導(dǎo)致的冷卻不均;
噴淋壓力:0.3-0.5MPa,呈扇形覆蓋鋼套表面,避免局部過(guò)冷。
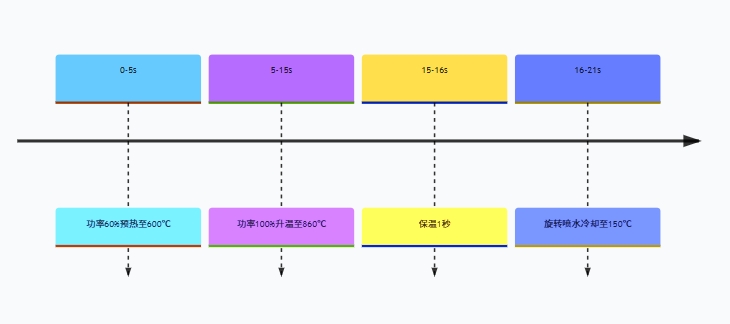
預(yù)變形補(bǔ)償:根據(jù)模擬計(jì)算,對(duì)易變形部位(如薄壁段)提前施加反向應(yīng)力;
應(yīng)力釋放槽:在非關(guān)鍵部位開(kāi)設(shè) 0.5mm 深槽,引導(dǎo)應(yīng)力集中釋放;
后處理時(shí)效:淬火后 200℃低溫回火 2 小時(shí),消除殘余應(yīng)力 30-50%。
指標(biāo) | 高頻淬火(鋼套) | 鹽浴淬火 | 滲碳淬火 |
---|
硬化層均勻性 | ±0.1mm | ±0.3mm | ±0.2mm |
變形量 | ≤0.05mm | ≥0.15mm | ≥0.1mm |
生產(chǎn)效率 | 10-30 秒 / 件 | 10-20 分鐘 / 件 | 4-6 小時(shí) / 件 |
能耗 | 0.2-0.5kWh / 件 | 2-5kWh / 件 | 10-15kWh / 件 |
材質(zhì):20CrMnTi 鋼套(Φ12×35mm)
工藝:300KHz 超高頻加熱,硬化層 0.8mm,硬度 58-62HRC
效果:耐磨測(cè)試顯示,使用壽命從 5 萬(wàn)公里提升至 20 萬(wàn)公里,氣門漏氣率下降 70%
挑戰(zhàn):Φ100×500mm 長(zhǎng)徑比 5:1,傳統(tǒng)淬火變形超 0.2mm
解決方案:分段式感應(yīng)器(上中下三線圈),50KHz 中頻加熱,旋轉(zhuǎn)冷卻(60rpm)
結(jié)果:變形量 0.04mm,直線度≤0.02mm/m,滿足精密注塑機(jī)要求
多工位聯(lián)動(dòng):配備轉(zhuǎn)盤式上料機(jī)構(gòu),實(shí)現(xiàn)高頻淬火機(jī) 24 小時(shí)連續(xù)生產(chǎn),某軸承廠應(yīng)用后產(chǎn)能提升至 2000 件 / 班;
參數(shù)自學(xué)習(xí):通過(guò) AI 算法分析歷史數(shù)據(jù),自動(dòng)優(yōu)化新批次鋼套的加熱功率與冷卻時(shí)間,使首件合格率從 85% 提升至 98%。
感應(yīng)器維護(hù):每周用鹽酸溶液(5% 濃度)清洗線圈水垢,保持冷卻水路流量≥15L/min;
頻率校準(zhǔn):每月用示波器檢測(cè)高頻電源輸出波形,頻率漂移超過(guò) ±1% 時(shí)需調(diào)試;
導(dǎo)磁體更換:鐵氧體導(dǎo)磁體每 5000 次使用后磁導(dǎo)率下降 10%,需及時(shí)更換以保證加熱均勻性。
鋼套高頻淬火通過(guò)熱控技術(shù)與防變形設(shè)計(jì)的深度融合,實(shí)現(xiàn)了從 "經(jīng)驗(yàn)工藝" 到 "數(shù)字工藝" 的跨越。從汽車零部件到高端裝備制造,其精密控制能力正成為提升機(jī)械產(chǎn)品可靠性的核心技術(shù)之一。如需針對(duì)具體鋼套規(guī)格(材質(zhì)、直徑、長(zhǎng)度)制定淬火方案,可提供詳細(xì)參數(shù),我們將協(xié)助設(shè)計(jì)專屬的感應(yīng)器配置與工藝曲線。